Robotic Welding – Qualifications
That Make the Difference!
We don’t just understand the need for safety and quality. We live it, too.
Quality, safety, 5S, on-time delivery, and competitive pricing are core values of our Big Gun Robotics team. Our qualifications allow us to deliver on those values to the benefit of our employees and our customers. The quality of robotic welding relies on both the quality of materials and the consistency of workflow. Once these issues are systematized, however, a robotic device can perform exceptionally high-quality, efficient welds much more consistently than even the most experienced professionals.
ISO Compliant
Robotic Welding Verification Through Ultrasonic Testing
AWS Certified Welders
QMS System
EPA Registerd Site
ERP Utilization
Our ERP implementation provides efficient and current monitoring of the manufacturing processes to further improve efficiency and on-time delivery. ERP—short for Enterprise Resource Planning—allows your businesses to run more smoothly, but it needs to be used efficiently. Fortunately, we at Big Gun Robotics understand ERP Utilization and how to maximize its potential on our customers’ behalf.
Six Sigma
Precision welding requires more than simply fusing two pieces of metal together. Achieving a high level of precision with the process often involves using Six Sigma to ensure the highest possible quality and yield from every weld. This precision welding methodology has several key components that work together to improve manufacturing efficiency, especially when it comes to complex assemblies such as those used in aircraft, aerospace, automotive and defense industries. Our team is well versed in Six Sigma, and by identifying potential problems early on, we can help prevent defects before they happen.
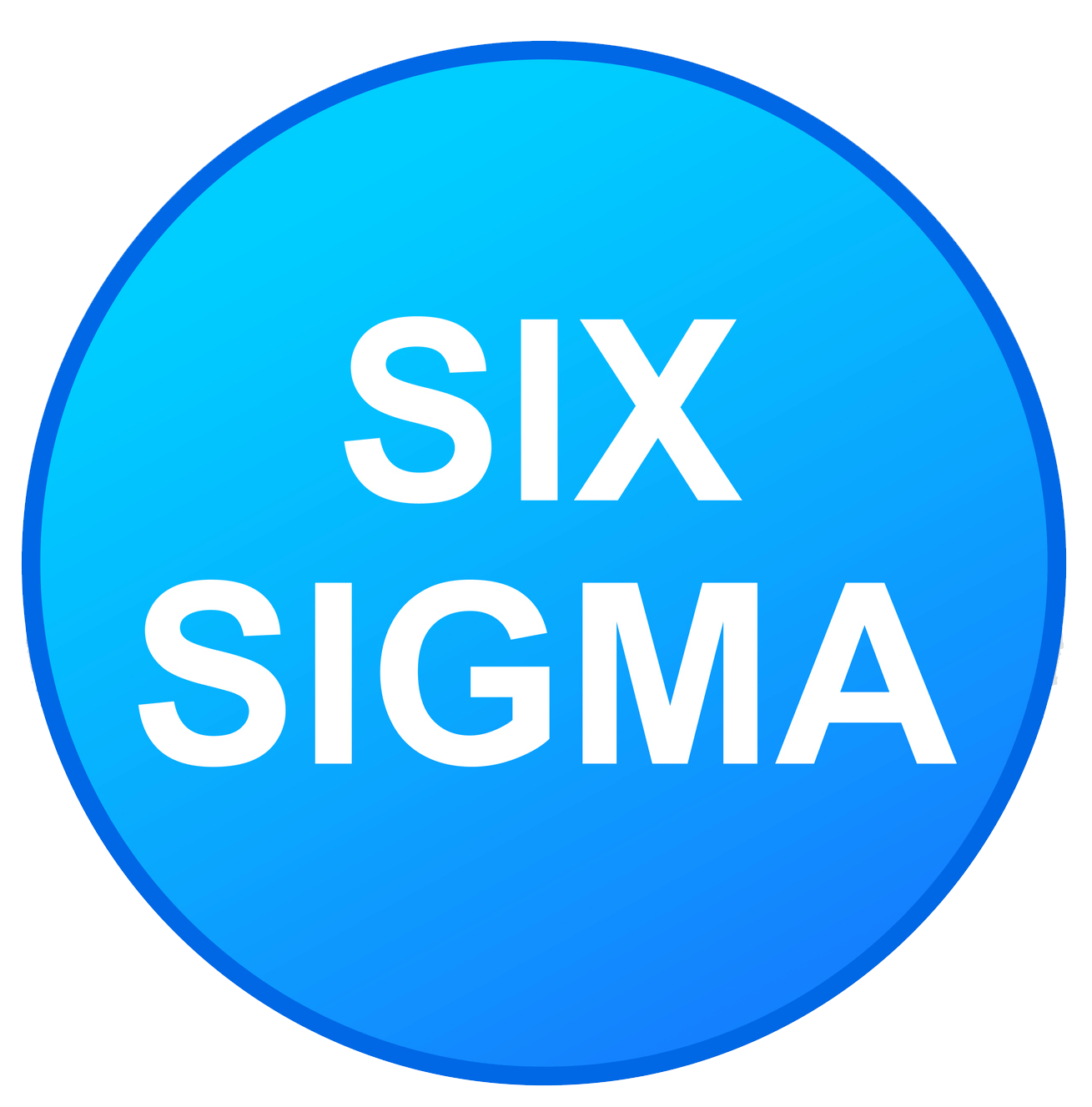
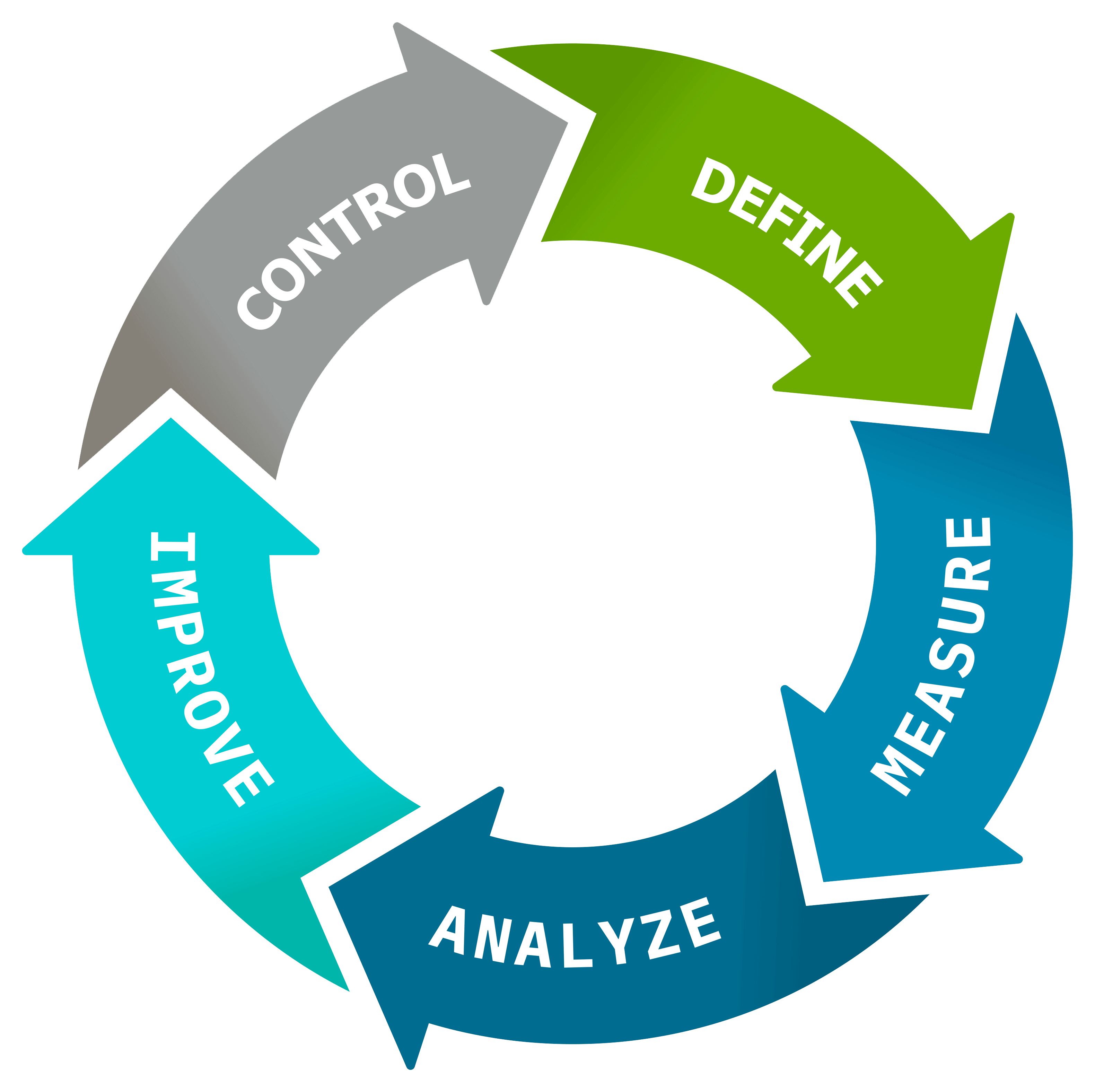
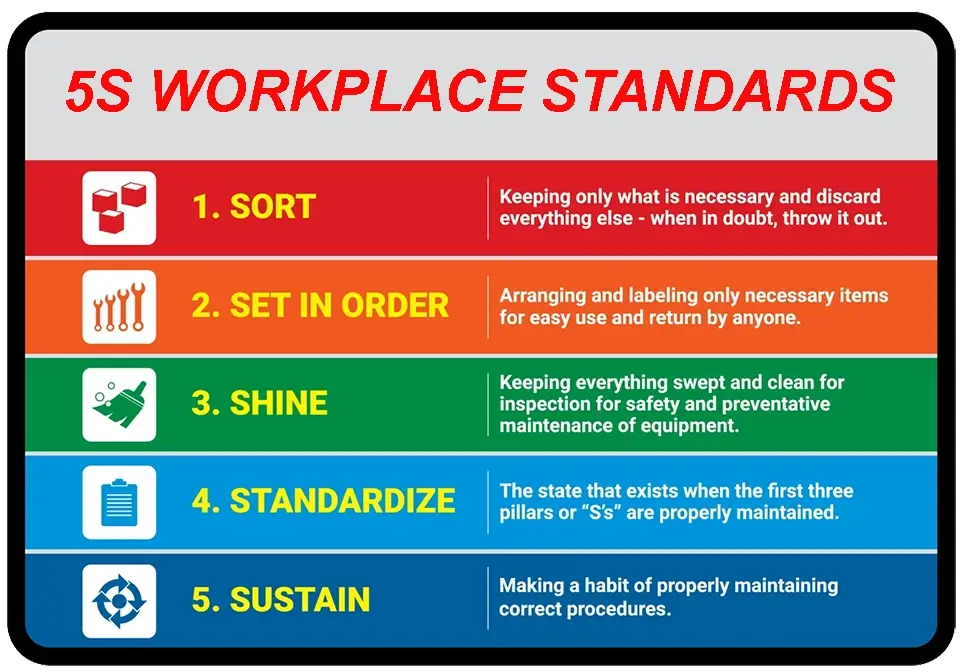
Safety Standards
Manufacturers are held to strict safety standards in order to protect their employees, and Big Gun Robotics is no different. On an even broader scale, we also adhere to OSHA (Occupational Safety and Health Administration) regulations that outline required safety training, as well as appropriate equipment usage. Our safety policy and procedures combine to help us reach our goal of zero accidents and zero injuries.
5S
5S is a workplace organization methodology that centers on cleanliness and preventive maintenance. In addition to safety, 5S also has a positive impact on productivity. By implementing these practices, our employees are safer and more efficient when completing tasks. Our 5S and safety policies/procedures combine to help us reach our goals as a company to always be safety-minded and help eliminate accidents with an organized work environment. Strict adherence to safety policies empowers our team to deliver products to our customers safely and efficiently.